Full-Featured Software/Hardware Motor Control Design Ecosystem Accelerates Time-to-Market
With modern MCUs/DSCs, IDEs, and an ecosystem of software libraries, code examples, application notes, reference designs, and development/evaluation boards, even novice motor control designers can rapidly develop and deploy professional solutions without having to...
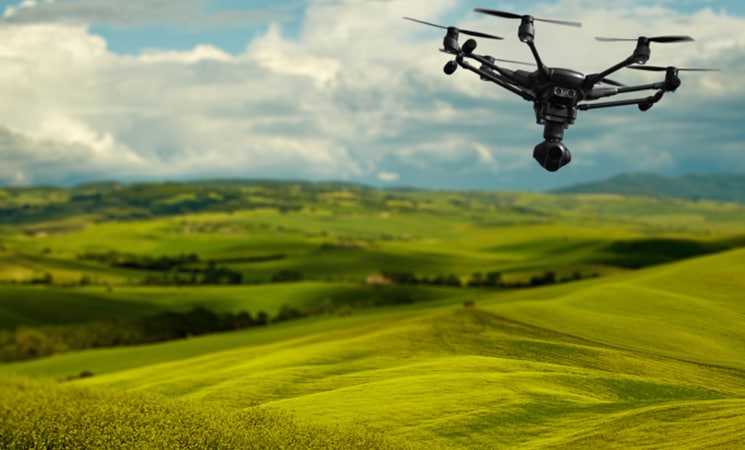
Abstract
Electrical motors are used in a wide range of applications, from low-cost and low-complexity appliances, to life-saving medical appliances, to multi-million dollar industrial robots. A new wave of complex and efficient motor types are gradually being adopted in a wide range of markets. Hence, designing and programming the next generation of motor control systems can be as complex as the end-application. Microcontrollers (MCUs) and Digital Signal Controllers (DSCs) can be used to enable advanced motor control features but are also challenging to prototype and design. Microchip offers hardware and software solutions, alongside a host of design resources and materials, that empower motor control designers to meet stringent design requirements and accelerate their time-to-market.
This article discusses the trends and challenges associated with modern embedded motor control applications. Moreover, this article details how Microchip has developed a portfolio of MCUs, MPUs, and DSCs, as well as an array of professional-grade software and development resources, that address these challenges and enable motor control designers and developers to build higher performing solutions while reaching the market faster.
Motor Control Trends and Challenges
Several key markets and applications are driving the demand for more efficient, smaller form factors, and more reliable motors that also offer a greater degree of control than previous motor technologies. The demand in the HVAC, medical, automotive, and robotic sectors have led to increased development and adoption of Brushless DC (BLDC) motors, Permanent Magnet Synchronous Motors (PMSM), and switched reluctance motors (SRMs). Moreover, both commercial, home appliance, and construction applications are also increasing demand for BLDC and more efficient AC motors.
Though these new motor types tend to offer higher energy efficiency and controllability, these new motor types also require more sophisticated control electronics, complete with precise timing, sensing, and complex feedback algorithms compared to prior motor technologies. Additionally, the competitive nature of the industry, along with space constraints for many of these applications, place additional design burdens on motor OEMs to keep costs low and motor footprints small--all without sacrificing performance.
Given the nature of many of these modern motor applications and the speeds at which high-efficiency motors can operate, motor control electronics are being required to maintain more accurate speed and position measures, while also ensuring noise immunity. For industrial, automotive, and medical applications, reliability under stress and in extreme environments is also essential, which is a more significant challenge given the increased complexity of motor control systems.
Due to the complexity and recent adoption of new motor types, it would stand to reason that long development cycles could be expected. However, the competitiveness of the motor market is encouraging OEMs to develop new and more efficient motor systems in much shorter design cycles than in prior years. This task is compounded in difficulty, as motor control systems are essentially impossible to breadboard, and prototype designs must proceed mostly with extensive simulations and models before hardware can be assembled. The expertise necessary to proceed with this process leaves a steep learning curve for the uninitiated.
For these reasons, Microchip has invested substantial resources in developing several lines of MCUs/DSCs targeted at addressing these embedded motor control challenges. Beyond that, Microchip has also pioneered a host of unique software tools, libraries, and reference designs to complement their professional-grade software ecosystem and enable a more streamlined and robust software development process.
MCU and DSC Features Geared Toward Motor Control
Given the particular nature of each motor control application, a wide selection of MCUs/DSCs is beneficial in achieving an optimized design. With many vendors only offering a small selection of motor control MCUs/DSCs, a design team may have to prototype hardware and software for several different vendors before narrowing down their choices. With Microchip’s expansive selection of MCUs/DSCs that have a wide range of highly integrated motor control features, this hardware guess-and-check is no longer necessary. Microchip makes available MCU/DSC solutions that are built for modern 2-phase AC, 3-phase AC, and DC, including the latest motor technologies, BLDC, PMSM, Switch Reluctance (SR) motors, as well as legacy motor technologies. Given the increasing complexity and constraints on these new high-performance motor technologies, Microchip’s motor control devices are also equipped with unique features to enhance integration, reduce footprint, reduce bill-of-material costs, boost efficiency, and ease development.
The wide selection of MCUs/DSCs from Microchip are available in extremely small packages, which allow for much smaller electronics board sizes. Additionally, these devices are equipped with analog, digital, and motor control hardware features that are typically external to the processing/control devices, such as Pulse-width Modulation (PWM) outputs, high speed Analog-to-digital Controllers (ADCs), Operational Amplifiers (Op-amps) for current gain, Comparators, Digital-to-Analog Converters (DACs) for feedback loops, and some Microchip System-in-package (SiP) DSCs are further outfitted with integrated MOSFET gate drivers.
Furthermore, Microchip makes available motor control hardware with Core Independent Peripherals (CIPs) and specialized peripherals for motor control that facilitate a decrease in processor burden and improve the performance of distinct motor control functions. For example, the dsPIC33C family of DSCs comes with integrated Intelligent Analog and CIPs, including ADCs, DACs, PWMs, Programmable Gain Amplifiers (PGAs), Analog and Digital Comparators, a Quadrature Encoder Interface (QEI), two CAN Flexible Data-rate (FD) protocol modules, Configurable Logic Cells (CLCs), and SENT protocols. Advanced peripherals and MCU/DSC designs enable complex motor-specific functions, such as Sinusoidal-less Field Oriented Control (FOC) for low noise and high-efficiency operation of AC motors, High Frequency Injection (HFI) for advanced 3-phase rotor sensing, wind-milling techniques for smoother starts, and the ability to accommodate complex torque control algorithms. These integrated capabilities help to reduce the BOM complexity, PCB footprint, power, and susceptibility to interference of motor control electronics built with Microchip MCU/DSCs.
Safety for embedded motor applications, even for low-cost commercial appliances, is essential. Safety features only become more critical for industrial and automotive applications. Device reliability is an often overlooked, but always critical, aspect of safety that also impacts brand image. Many embedded motor device manufacturers sacrifice safety and reliability for cost, as they may be under the opinion that devices with Functional Safety features and automotive-qualified silicon are inaccessible and expensive. Microchip offers competitive MCUs/DSCs that conform to a variety of Functional Safety levels (ISO 26262) and automotive qualifications (AEC Q100 Grades); some have operating temperature thresholds of 150ºC for extreme applications.
Go Here to View: Embedded Motor Control Device Feature of Microchip MCU-DSC
Professional Development Tools Empowering Embedded Motor Developers
An embedded device is only as good as the software tools and resources available to designers and developers, and this is especially true for motor control applications. As one of the main hurdles is prototyping early motor control designs, development boards with the same hardware and similar capabilities to a prototype board are critical in refining motor control algorithms and prototyping safety features. Hence, Microchip offers development boards compatible with a wide selection of MCUs/DSCs with advanced motor control features. These boards include the SAM V71 Xplained Ultra Evaluation Kit, PIC32MM Curiosity Development Board, and Explorer 16/32 Development Kit. These development systems are all extensible, and the code used for early prototyping and evaluation with these systems can easily be reused for future prototyping, refining, and even production. Furthermore, Microchip makes available several kits and demonstration boards that are designed toward specific applications, such as the 3-phase BLDC Sensorless Fan Controller Demonstration Board, and MCHV-2 High Voltage Motor Control Development Board.
Alongside these demonstration and evaluation systems are complementary application notes and resource documentation that enables a designer and developer to overcome steep motor control learning curves and more rapidly deploy new designs. These application notes cover low-voltage to high-voltage applications, including algorithms, designs, code, and application-specific reference designs. For example, Microchip’s Air Conditioner Reference design, based on the dual-core dsPIC33CH family of DSCs, includes documentation and hardware design for high power PFC, condenser fan, compressor motor control, and additional inter-faces with sensors, communication, and valve drives. Similar reference designs exist for drill torque, drone, and other applications. Also, Microchip makes an extensive array of code examples, software libraries, and application notes available to designers and developers, many of which provide quick answers to the hard questions of embedded motor control and provide professional-level solutions and insights useful for even expert motor control designers.
A software and design tool flow for motor control can be as complex as a C-code mathematics environment based on manual entry, to an enterprise-grade and Multiphysics simulation environment. Microchip has a solution that costs as much as the C-code mathematics environment and enables ease of use beyond a sophisticated simulation environment. motorBench® is a GUI-based FOC software development tool for both low-voltage and high-voltage systems, which aids a motor control designer in accurately measuring, calculating, tuning, and generating C-code for the electrical and mechanical motor parameters. This C-code could be used in any IDE, but it is especially designed to work with MPLAB® X Integrated Development Environment (IDE), which is further complemented by accessible software libraries and code examples from Microchip staff and the professional community. Moreover, Microchip makes available device blocks which are compatible with MPLAB/Simulink® simulation systems, which can also be used to generate C-code for motor control.
Next Generation of Hardware Motor Control DesignThough designing and developing software for embedded motor control applications has historically been challenging and mainly driven by niche analog and power design, the latest generation of motor control MCUs/DSCs and software resources is changing this paradigm...with modern MCUs/DSCs, IDEs, and an ecosystem of software libraries, code examples, application notes, reference designs, and development/evaluation boards, even novice motor control designers can rapidly develop and deploy professional solutions without having to scale a steep learning curve and spend years getting a product to market.