Silicon for Digital Power Adds Flexibility and Performance
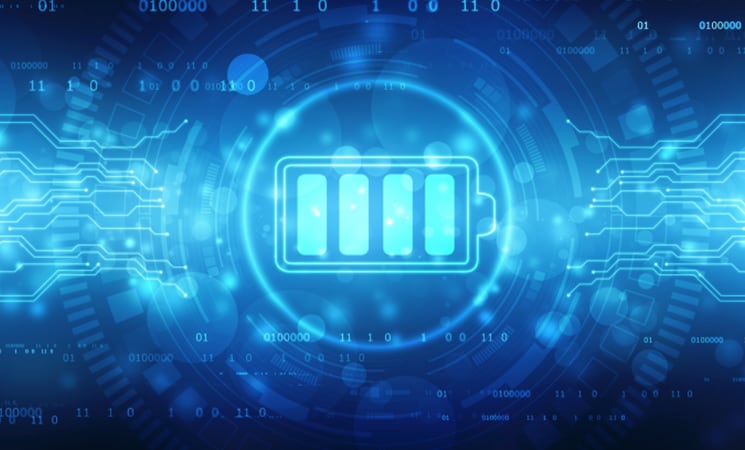
Abstract
The latest efficiency standards, along with the ability to adapt to continually changing environmental effects, present many challenges for traditional analog power design. The transient behavior of modern power electronics, environmental considerations, and design complexity for modern electronics requires a more flexible design approach that can account for these new variables. Digital power conversion and control solves many of the challenges facing designers; however, many designers struggle to adapt their analog domain knowledge to the latest digital systems and work with developers to implement competitive product features.
Microchip has responded to these considerations by providing an extensive digital power ecosystem, complete with Microcontrollers (MCUS) and Digital Signal Controllers (DSCs), cutting-edge power conversion features, fully functional reference designs, freely available advanced design resources, and leading-edge software solutions with unique tools.
The Growth of Diverse Electrical Power Technology
There is a growing trend to incorporate electrical power systems into many applications previously powered by combustion, mechanical, or compressed air. Moreover, there is an increasing number of distributed power systems, such as battery-based grid backup, renewable energy, energy storage, uninterrupted power supplies, and more being deployed to reduce fossil-fuel consumption and increase power system efficiency. The factors fueling the Information Age (data centers/server power supplies) are electrical-power hungry, and stiff competition limits placing a greater emphasis on reducing expenses. Much of the focus of modern electrical power systems is to enhance efficiency, optimize delivery, and to accommodate a broader range of Direct Current (DC) and Alternating Current (AC) systems.
With the expanding diversity of electrical power technology, as well as stricter requirements for efficiency, innate custom analog power designs are not optimal for many of the latest power applications and implementations. Furthermore, the rapid pace of the electronics and electrical systems markets are rapidly churning through new certifications and standards. Now, these are even more challenging to accommodate with analog power design. Therefore, many OEMs are turning toward digital power solutions to rapidly augment their current electrical power product portfolios. Fully digital solutions provide a more adaptable and efficient platform to accommodate the latest electronics and electrical systems.
As digital power is a recent advancement, and outside the domain of many traditional analog power designers, there are many designers unfamiliar with the technology. Microchip is remedying this by providing innovative solutions that mitigate many of the traditional challenges associated with electrical power design, along with educating engineers and designers about the future of digital power technology.
Power Design Challenges
Power design is transitioning from a field dominated by a few expert analog designers to an arena blending software, digital, and analog design. This shift is happening in response to market factors and new technologies that enable the use of digital power solutions that address many of the challenges posed by electrical power design. A key area of this challenge is ensuring a highly efficient and reliable power system operation while accounting for diverse and often fluctuating conditions. Achieving efficiency over widely varying load conditions is a major aspect of this challenge.
Though analog systems can often be designed to be extremely efficient in a narrow range of operating conditions, these systems tend to suffer inefficiencies when accounting for a range of operating conditions. Moreover, if requirements change, an analog power system may require a complete redesign, or at least substantial design changes, which amount to delayed design cycles and a longer time-to-market. Attempting to future-proof analog power designs also tends to add significant costs, and in many cases isn’t viable. Digital power technologies are increasingly employed to enable a more flexible and efficient design approach given the transient nature of modern electrical power system operation.
However, digital power system development requires knowledge on both analog power technology as well as digital control systems theory. Often multiple teams of designers and developers are working on an individual power system, each having their own set of requirements and demands of limited Microprocessor (MPU) or DSC resources.
As is commonly understood, software updates often lead to system downtime. In industries that measure their margins to several decimal places, minimizing downtime is essential for electrical power systems. Given the complexity of the firmware, certification, and verification requirements, this is no easy feat with any software-driven technology.
Digital Power Solutions Enable Efficient and Robust Power Design
Digital power technologies often leverage software-driven switching power designs and highly integrated components to improve efficiencies and reliability. Designing digital power systems that account for maintaining efficiency under various load conditions, and accounting for environmental factors, such as external and internal temperatures, is possible with adequate software development.
For relatively simple systems (less than 100 watts), where legacy analog control and conversion need to be replaced, an 8-bit MCU may be adequate. For example, Microchip’s 8-bit MCUs geared toward digital power applications are alluring for highly efficient and reliable standings with analog Boost, Buck, Boost/Buck, Flyback, and SEPIC power converter topologies. Moreover, many of Microchip’s 8-bit MCUs also include integrated peripherals, such as Peak-Current Mode Controller (PCMC), ramp generator, slope compensation circuits, and others. These integrated peripherals help to reduce the burden on the main processor while also enhancing reliability. Designs using these MCUs effectively close the control loop with dedicated hardware that is supervised by the 8-bit processing core.
For more complex power systems that would benefit from more sophisticated or adaptive/predictive algorithm control/conversion, 16-bit MCUs or DSCs are a more capable choice. Software-based algorithms, such as predictive, adaptive, and even non-linear functions, enable a system to achieve the highest levels of efficiency that would be difficult - if not impossible - to achieve with simpler controllers.
Many of Microchip’s dsPIC® DSC families also include integrated digital power peripherals, such as high-speed Analog-to-Digital Converters (ADCs), Digital-to-Analog Converters (DACs), waveform generators, analog comparators, and Programmable Gain Amplifiers (PGAs) or op amps. These integrated peripherals reduce main processor burden, reduce latency, and ease development burden. As reliable communication is also a concern between sensors, peripherals, controllers, actuators, and more, Microchip’s latest dsPIC33C family also includes dual CAN FD communication peripherals. The CAN FD communication standard is common amongst automotive and industrial power applications where reliability and increased bandwidth are critical.
Moreover, Microchip offers another feature with several MCUs and DSCs that further mitigates the main processor burden and also helps with development: dual-core digital power MCUs and DSCs. Resources of both cores can be intelligently balanced to optimize performance under load and manage latency, and the way the cores are partitioned allows for independent development by separate software teams along with easy code integrations.
Developers working with Microchip’s MCUs and DSCs receive additional aid with an extensive ecosystem of design resources. These resources include a particular topology-independent tool for digital power design, the Digital Compensation Design Tool (DCDT), which is a GUI integrated into MPLAB® X Integrated Development Environment (IDE). The DCDT simplifies the process of calculating digital compensator coefficients and provides several control system performance analysis features by incorporating all delays and feedback gains. Additionally, the DCDT produces analog-friendly, closed-loop performance plots, such as Bode, root locus, and Nyquist. Lastly, the DCDT will automatically calculate scaling parameters, compensator coefficients, and generate software files used with Microchip’s free SMPS Control Software Libraries.
Another development tool freely provided by Microchip is the MPLAB Code Configurator. This tool is based on a graphical programming environment, which is easy to use for analog designers transitioning to digital power, and seamlessly generates easy-to-understand C code. This code can then be readily inserted into a project, with MPLAB X IDE or even Microchip’s cloud-based development tool MPLAB Xpress IDE. With a Microchip MCU or DSC, developers also have access to Microchip’s Compensator libraries and code examples, which are professionally developed and tested by application experts.
These libraries and code examples can help a designer or developer rapidly adapt from analog design to digital, and otherwise reduce the learning curve of digital power design. Another resource that can accomplish this is Microchip’s reference designs and development kits. The library of digital power reference designs includes wireless power demonstrations, AC/DC converters, low-voltage PFC kits, digital pure sine wave UPS designs and other DC/DC and AC/DC converter designs and kits.
As reliability is a crucial consideration for many power applications, MCUs and DSCs with compliance to rigorous industrial and automotive standards is often a base qualifier. Some of the strictest standards for power electronics are automotive standards, such as Automotive Safety Integrity Level (ASIL) and automotive Class B compliance. Microchip addresses this by making MCUs and DSCs available that are automotive-qualified silicon and incorporate peripherals that meet and exceed Functional Safety qualifications. Furthermore, Microchip has developed MCUs and DSCs with live update capabilities that allow for “always on” Over-the-air (OTA) firmware updates. This feature empowers developers and designers to eliminate downtime when upgrading software or troubleshooting a digital power design. For many power conversion applications in industries that avoid downtime due to high costs of poor up-time ratings, this feature enhances reliability and can provide significant savings.
Designs With Digital Power Capabilities in Mind
Digital power systems demonstrate many advantages over analog power systems for modern electrical power requirements. The demand for the highest efficiency over widely varying load conditions while accounting for environmental factors and shifting requirements, and demand for higher efficiencies have increased the adoption of digital power technologies, which create challenges for traditional analog power designers. Microchip’s digital-power capable MCUs and DSCs help to alleviate these burdens and provide integrated peripherals, feature, and a wealth of options to power designers and developers. Moreover, the development resources and tools available from Microchip aid in a smoother transition from traditional power design to modern software-driven development.